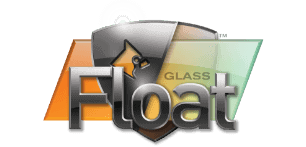
CARDINAL FG COMPANY
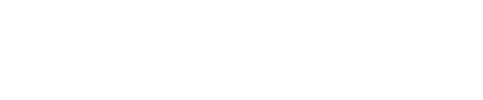
Superior Flat
Glass
Quality from the Beginning
Top of the line residential window manufacturers rely on a constant supply of high-quality float glass. At Cardinal FG Company, such quality is what you can expect–our seven U.S. FG facilities will provide it for you every time.
The pursuit of perfect glass
Cardinal looks ahead of the industry by using new technologies that will meet even tomorrow’s marketplace. Our constant growing spirit takes glass manufacturing to a higher level. Our modern furnace design gives Cardinal an excellent system for producing float glass in a 24/7 environment.
The capabilities built into the process give our operations maximum flexibility to produce the many different thicknesses of glass – from 1.6 to 7mm that are required for the residential market.
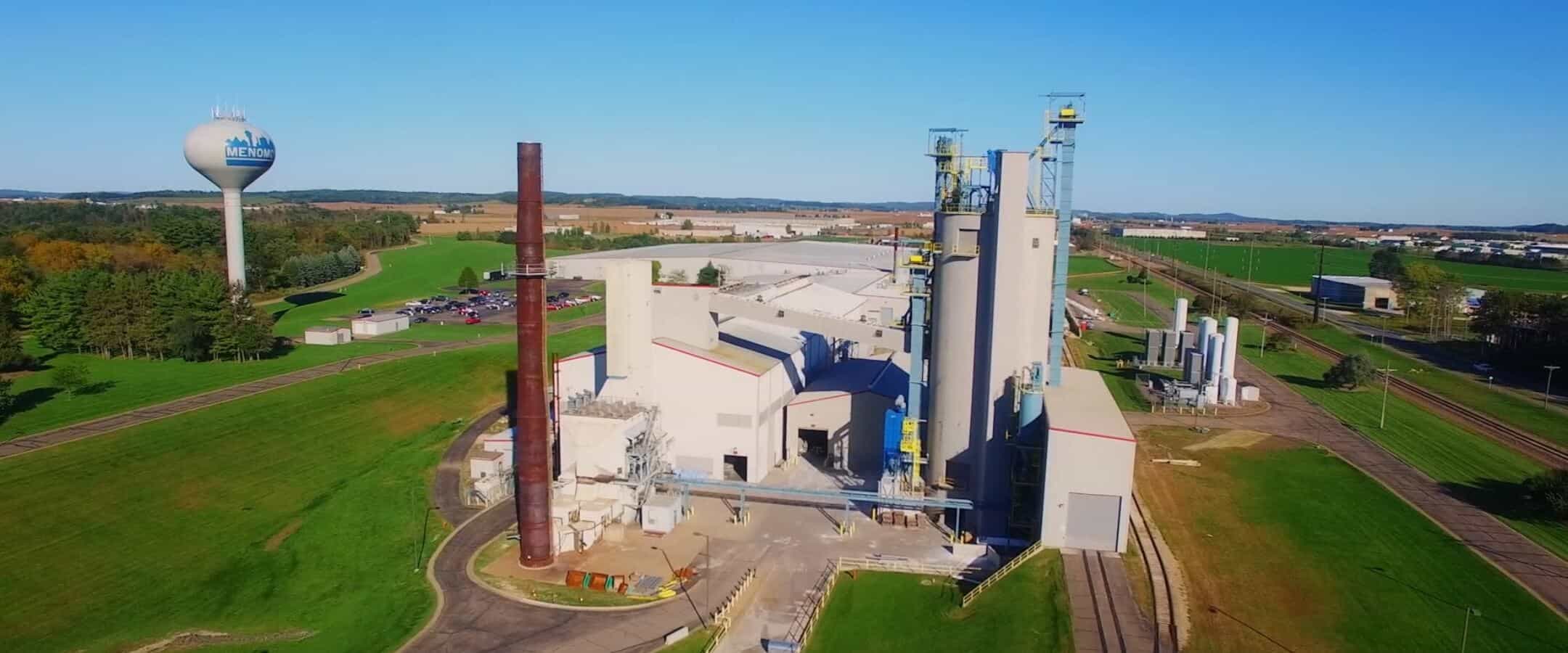
A vision of excellence from
production to shipping.
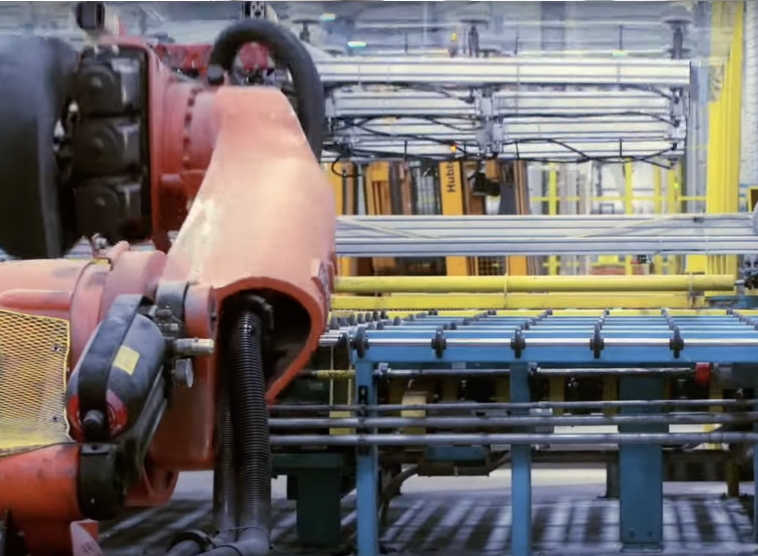
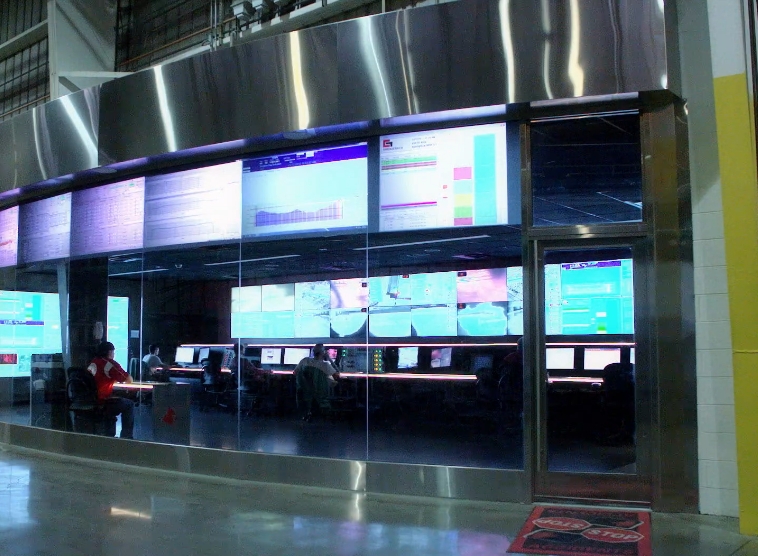
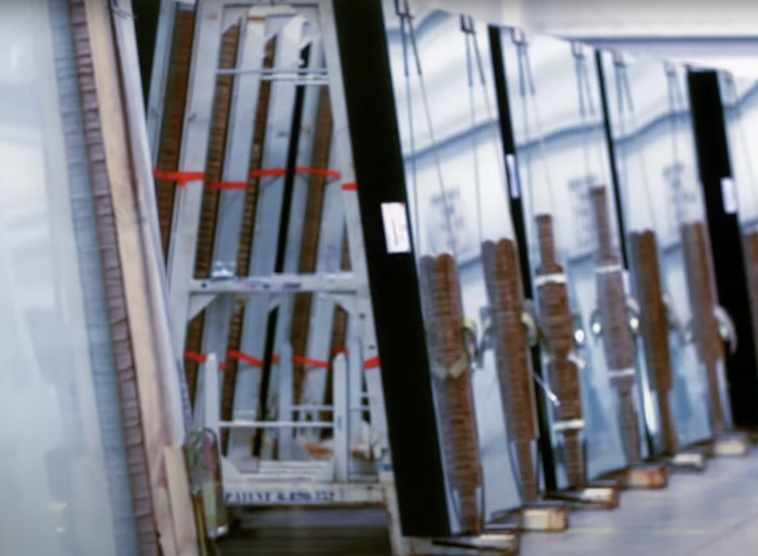
Intelligent Quality
Did you know?

Float glass plants are enormous–over 350,000 square feet under each roof.
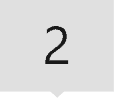
Each plant uses $500,000 of natural gas and $85,000 of electricity every month.
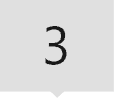
Float plants run nonstop 24 hours a day, 365 days a year.
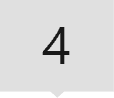
Each FG plant ships 35-40 trucks of glass every day, at almost 35,000 square feet per truck.
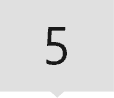
Glass is cut in sizes as small as 16″ x 20″ to as large as 130″ x 204″.
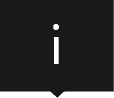
These systems as well as our industry-leading inspection processes are the assurance that Cardinal glass will exceed specification and expectation. Great glass helps make great windows, so manufacturing superior float glass is always our stated goal.
Additional Resources
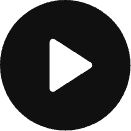
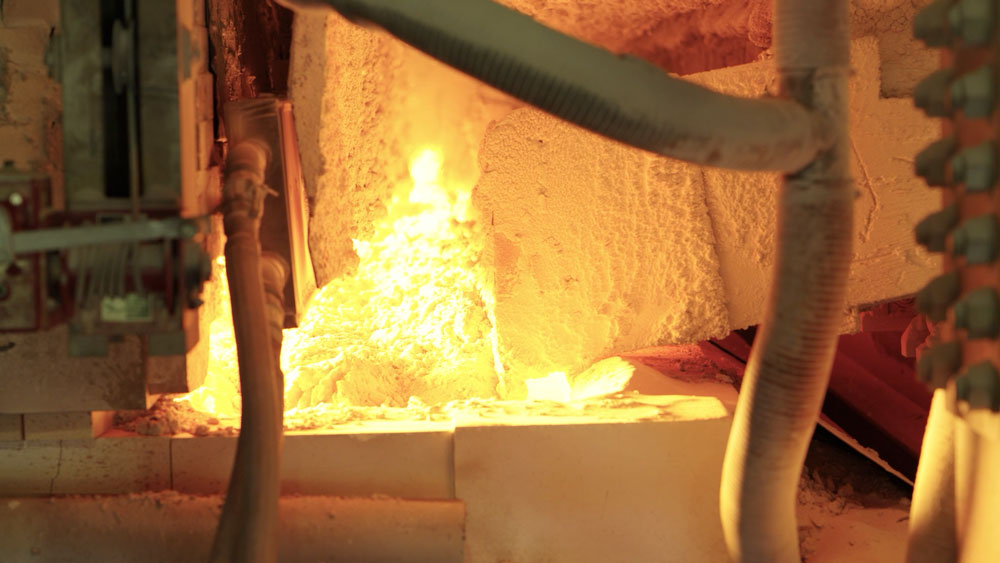